[논문리뷰] An adaptive approach for determining batch sizes using the hidden Markov model-3
이어서 진행해보자면,
다음 내용은
실험 시뮬레이션 및 결과 분석 (Simulation and Experimental Results)
논문에서는 HMM을 기반으로 배치 크기를 최적화하는 모델을 검증하기 위해 시뮬레이션 실험을 수행했다.
➡ 실험에서는 산업 로봇(MH, Material Handler)과 CNC 가공 기계(MP, Machining Processor)가 있는 제조 시스템을 고려하여 배치 크기를 결정하는 방식을 테스트했다.
실험 시스템 설명 (System Description)
시스템 개요
- 산업 로봇 (MH, Material Handler):
- 부품을 픽업하고, 가공 기계(CNC 머신)로 이동시킨다.
- 제품의 위치(Location)에만 영향을 미친다 (정확한 위치에 놓여야 함).
- CNC 가공 기계 (MP, Machining Processor):
- 부품을 절삭 가공한다.
- 제품의 치수(Dimensional Tolerance) 및 위치(Location Tolerance)에 영향을 미친다.
실험 목표
- 배치 크기 결정 모델이 실질적으로 제조 공정에서 어떻게 적용될 수 있는지 검증하기 위함이다.
- 공정 변동성(Variability)이 증가할 경우, HMM을 통해 이를 감지하고 배치 크기를 적응적으로 조정하는지 확인한다.
실험 과정
- 로봇(MH)이 부품을 집어 CNC 가공 기계(MP)로 이동시킨다.
- CNC 가공 기계가 부품을 가공한다.
- 가공된 부품의 품질 데이터를 수집하여, HMM을 통해 공정 상태를 예측한다.
- 다음 배치 크기를 결정한다(배치 크기를 늘리거나 줄일지 판단).
➡ 즉, 로봇이 배치를 이동시키고, CNC 가공이 완료되면 품질 데이터를 분석하여 배치 크기를 조정하는 방식이다.
시스템에서 사용된 변수 및 데이터 구조
각 장비가 제품 품질에 미치는 영향
- 로봇(MH)의 영향:
- 제품의 위치(Location) 정확도에 영향을 미친다.
- 만약 위치 오차가 커지면, 가공 정밀도도 영향을 받을 수 있다.
- CNC 기계(MP)의 영향:
- 제품의 치수(Dimension) 및 위치(Location) 정확도에 영향을 미친다.
- 기계의 성능이 저하되면, 제품의 품질 편차가 증가한다.
품질 데이터 변수 정의
- 제품 i의 관측 데이터 Oi. Oi=(Oi,1,Oi,2,...,Oi,F)
- 제품이 가공된 후 측정된 품질 데이터 (치수 및 위치 편차 포함).
- F는 제품의 품질 특성(예: 치수, 위치 등)의 개수.
- 상태 변수 (HMM에서 학습할 상태값)
- 로봇(MH)과 가공기(MP)의 상태를 각각 정의한다.
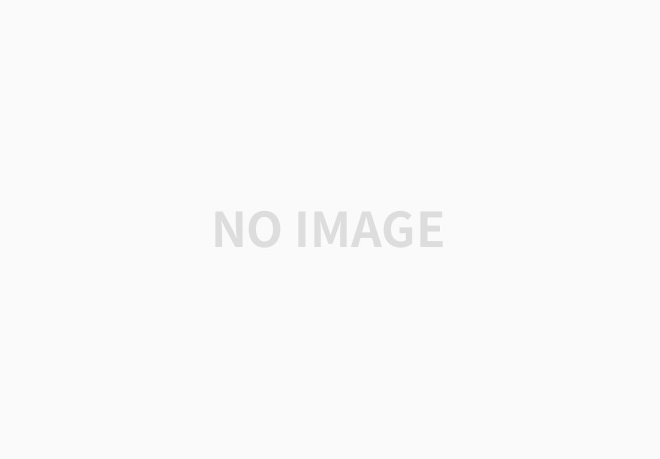
데이터 생성 과정
- 제품의 품질 데이터는 정규 분포(Gaussian Distribution)를 따르는 것으로 가정된다.
- HMM 모델을 적용하여, 시간이 지남에 따라 상태가 변화하는 과정을 반영한다.
실험 데이터 생성 과정 (Algorithm 1 - Generating Data Set)
실험 데이터 생성 목적
- 공정 변동성(Variability)이 랜덤하게 발생하도록 시뮬레이션하여, HMM이 이를 제대로 감지할 수 있는지 확인하는 것이 목적이다.
- 변동성은 포아송 분포(Poisson Process)를 이용하여 랜덤하게 발생하도록 설정된다.
데이터 생성 과정 요약 (Algorithm 1)
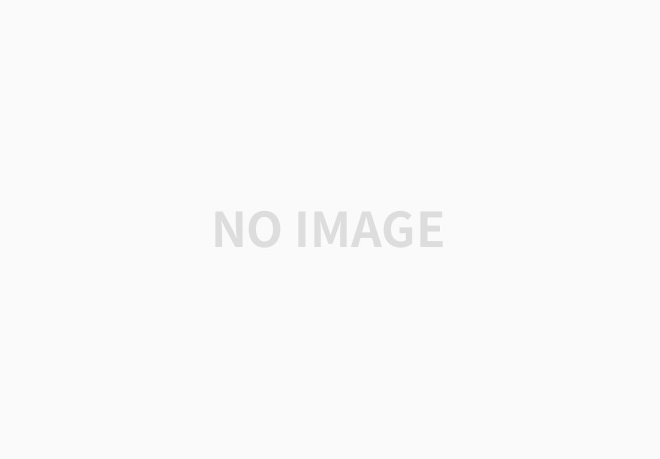
초기 설정:
input:
L : 공정 길이 (총 생성할 품질 데이터 수, 예: 500개 부품)
F : 제품의 품질 특성 수 (예: 위치, 치수 등)
C : 공정에 포함된 장비 개수
Θ₀ : 초기 품질 분포 파라미터 (정상 상태에서 시작함)
T^L, T^D± : 각각 위치/치수 허용 오차 (공차 tolerance)
i : 현재 공정의 위치 (i번째 부품)
p : 지금까지 발생한 이상(abnormality)의 횟수
RNₚ : 포아송 분포 기반으로 생성된 다음 이상 발생 시점 리스트
output :
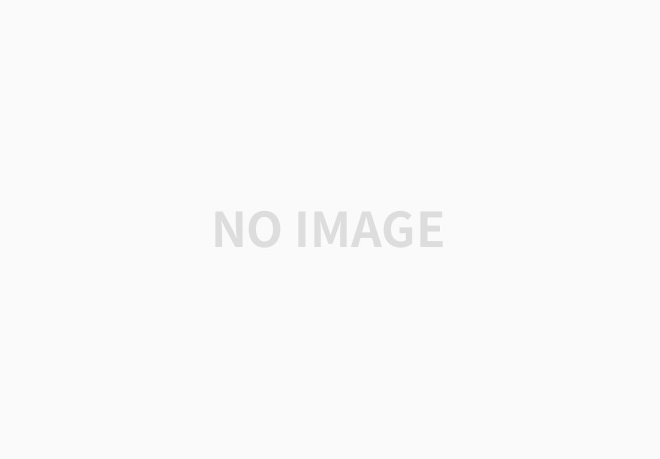
: 제품 1번부터 L번까지의 품질 데이터의 나열
Set i = 0, p = 1
i : 현재까지 처리한 제품 수
p : 발생한 이상 패턴 수
Initialize Θ₀
: 공정은 초기 상태로 시작 (정상 상태)
Generate random numbers corresponds to Poisson process
: 포아송 분포에 따라 공정 이상이 발생하는 시점을 RNₚ 배열에 저장
(예: RNₚ = [140, 220, 400] → 140번째, 220번째, 400번째 부품 이후 공정 상태가 바뀜)
while 루프 (i ≤ L)
💡Case 1: 아직 다음 이상 발생 시점 전 (i < RNₚ)
if p == 1:
generate observation
: 초기 상태, 아직 이상 패턴 없음 → 그냥 품질 데이터를 현재 파라미터 Θ로 생성.
else:
update value of parameters
generate observation
:
- 이상 패턴이 한 번 이상 발생한 경우
- 현재 파라미터를 비정상 상태로 업데이트 (예: 분산 증가, 평균 편향 등)
- 해당 상태로 관측 데이터 생성
💡Case 2: 새로운 이상 발생 시점에 도달 (i ≥ RNₚ)
select abnormal patterns, equipment, parameters...
update value of parameters
generate observation
set p ← p + 1
:
- 새로운 이상 발생
- 무작위로 어떤 장비에 어떤 이상이 발생할지 결정함
- 예: MP의 위치 분산 증가, MH의 위치 편차 발생 등
- 이를 기반으로 파라미터 업데이트
- 해당 상태에서 관측값 생성
- 이상 발생 횟수 p를 1 증가시킴
결과적으로,
L개의 제품에 대한 품질 데이터 {O_i}을 생성했다.
이 데이터는 시간이 지날수록 공정의 변동성, 이상 발생을 반영한다.
HMM 학습 및 배치 크기 최적화 테스트에 사용할 수 있다.
➡ 즉, 공정 변동성이 발생하는 환경을 가정하고, 이를 기반으로 배치 크기를 조정하는 실험 데이터를 생성하는 과정이다
최종 정리 – 실험에서 검증한 사항
실험 환경
- 산업 로봇(MH)과 CNC 가공기(MP)가 있는 제조 시스템을 가정함.
- 제품이 생산되면서 품질 데이터를 수집하고, HMM을 통해 공정 상태를 예측함.
- 변동성이 발생하면 배치 크기를 조정하여 품질을 유지하는 것이 목표.
HMM을 활용한 공정 모니터링
- 제품 품질 데이터를 통해 공정 상태(정상 vs. 비정상)를 실시간으로 감지함.
- 변동성이 감지되면 배치 크기를 줄여 불량률을 최소화함.
실험 데이터 생성 방법
- 공정 변동성이 포아송 분포를 따르도록 설정하여 현실적인 시뮬레이션을 수행함.
- 데이터는 정규 분포를 기반으로 생성되며, 공정 변동성이 커지면 품질 편차가 증가하도록 설정됨.
결과 분석을 위한 데이터 구조
- 로봇과 가공기의 품질 영향을 따로 분석할 수 있도록 변수 설정
- 위치 오차(Location Tolerance)와 치수 오차(Dimensional Tolerance)를 각각 분석
➡ 이 실험을 통해 HMM이 제조 공정에서 배치 크기를 조정하는 데 효과적으로 사용될 수 있음을 확인하려는 것이다.
실험 결과 분석 (Experimental Results) – HMM 기반 배치 크기 결정 모델 성능 검증
논문에서는 HMM 기반 배치 크기 조정 모델을 검증하기 위해 3000개의 시뮬레이션 데이터를 생성하고 실험을 진행했다.
➡ 기존 방식(PDP 기반 모델)과 비교하면서, HMM 모델이 배치 크기를 조정하는 능력이 얼마나 효과적인지 분석한다.
실험 개요
목적:
- HMM 모델이 실시간으로 품질 데이터를 분석하여 배치 크기를 효과적으로 조정할 수 있는지 확인한다.
- 전통적인 PDP 모델(Predefined Defective Probability Model)과 비교하여 성능 차이를 분석한다.
실험 방식:
- 3000개의 공정 데이터를 생성하여 HMM 모델을 학습한다.
- 새로운 3000개의 배치 데이터를 테스트하여 성능 평가한다.
- EM 알고리즘을 사용하여 매 500배치마다 모델 업데이트 진행한다.
- 다음 배치 크기 결정 시, 품질 데이터 기반으로 공정 상태를 예측하여 크기 조정한다.
- 기존 PDP 모델과 비교하여 불량률(Defective Rate)과 배치 크기(Batch Size) 비교한다
주요 실험 결과 분석
Fig. 6 – 배치 크기와 불량률 비교 (Proposed Model vs. PDP Model)
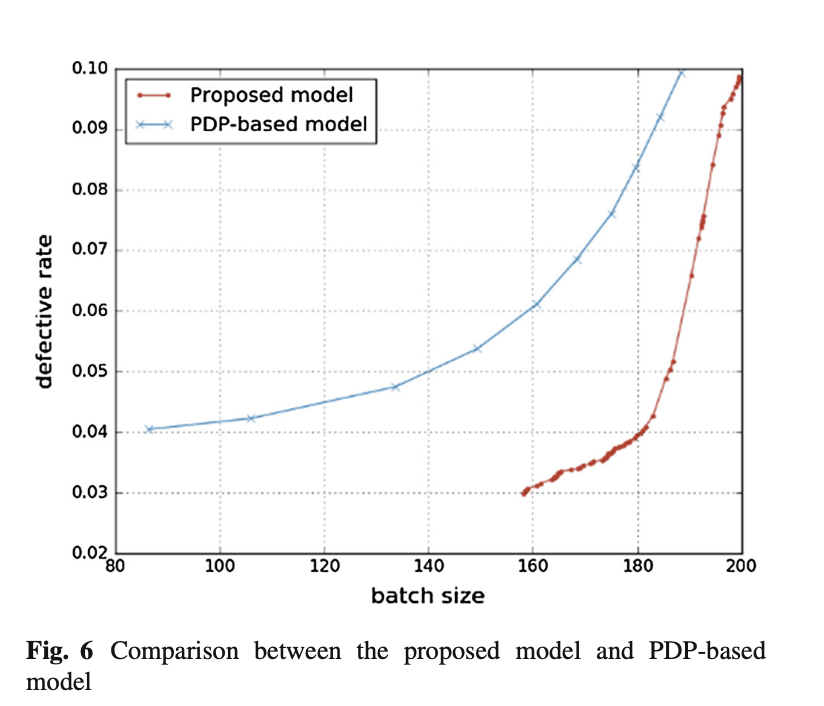
- 배치 크기(Batch Size) vs. 불량률(Defective Rate) 그래프
- Proposed Model (HMM 기반)은 더 큰 배치 크기를 유지하면서도 낮은 불량률을 기록했다.
- PDP 기반 모델은 배치 크기가 작고, 불량률이 상대적으로 높다.
의미:
➡ HMM 기반 모델은 품질 변동성을 실시간으로 예측하여, 불량률이 낮은 상태에서 배치 크기를 증가시킬 수 있다.
➡ PDP 모델은 사전에 정해진 불량률 기준을 유지하기 위해 배치 크기를 제한하는 방식이라 최적화가 부족하다.
Table 1 – 수치 비교 (Batch Size & Defective Rate)
- HMM 모델은 허용 불량률(δ 값)이 증가할수록 배치 크기를 크게 조정할 수 있다.
- HMM 모델은 기존 PDP 모델보다 배치 크기가 크면서도, 불량률이 더 낮다.
- PDP 모델은 불량률이 0.05 이상 증가하면서도 배치 크기가 작다.
의미:
➡ HMM 기반 배치 크기 조정 모델이 더 높은 효율성을 제공하며, 불량률을 낮추는 데 효과적이다.
Fig. 7 – Fast Stop (빠른 정지 기능)
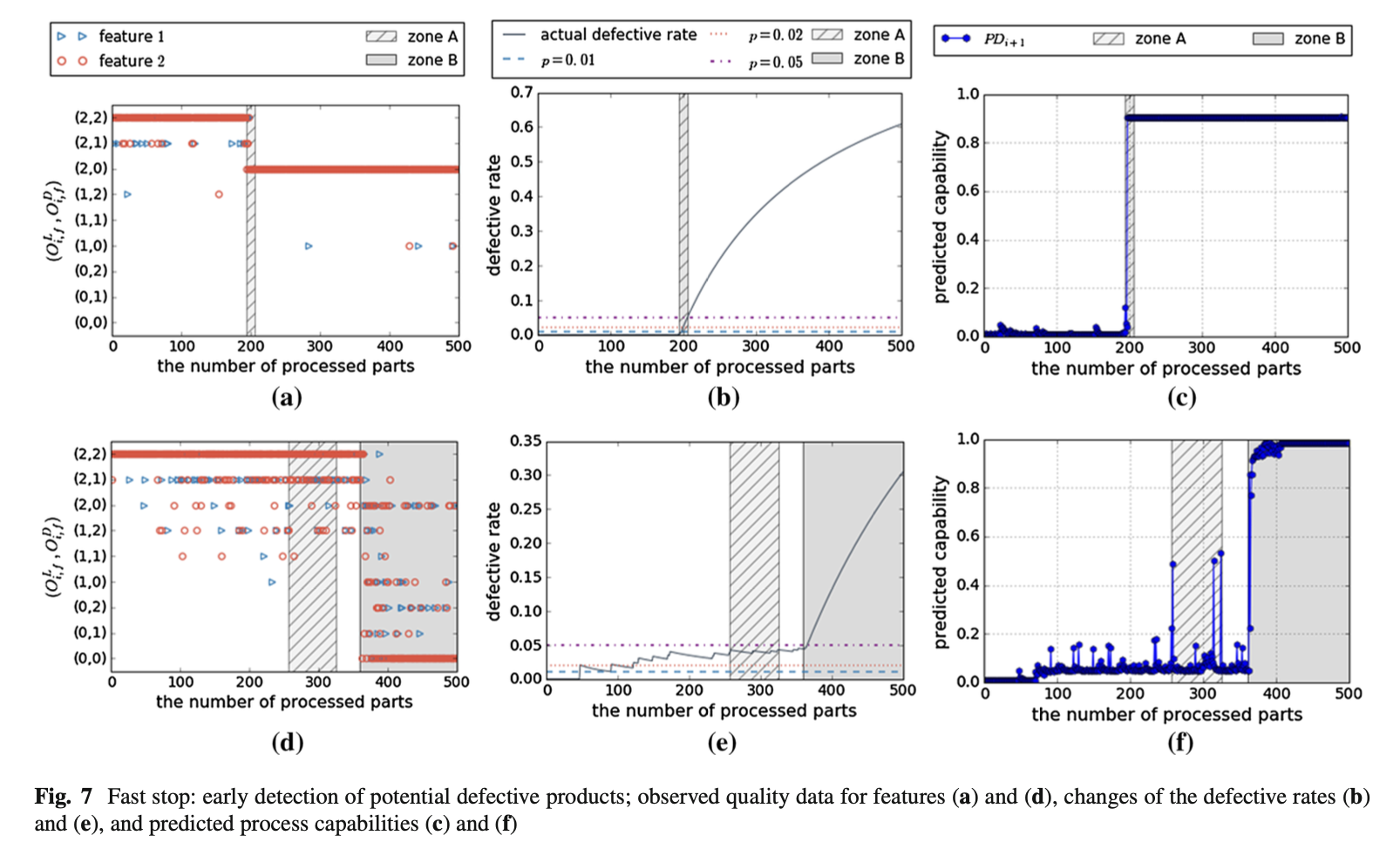
"Fast Stop"이란?
- HMM 모델이 공정 품질이 나빠질 것으로 예상되면 즉시 배치를 종료하고 재조정하는 기능이다.
- Fig. 7에서 Zone A에 들어서기 직전 HMM 모델(a-c)이 배치를 종료한다.
- PDP 모델(d-f)은 불량률이 0.05를 넘을 때까지 계속 생산하다가 늦게 조정한다.
의미:
➡ HMM 기반 모델은 불량률이 올라가기 전에 사전에 감지하여 배치를 종료하는 "Fast Stop" 기능을 수행할 수 있다.
➡ PDP 모델은 불량률이 0.05를 초과한 후에야 배치 크기를 조정하므로 반응 속도가 늦다.
Fig. 8 – Robustness (강건성, 견고함)

- HMM(a-c) 모델은 공정 상태가 좋은 경우 배치 크기를 증가시킬 수 있음.
- Zone A에서는 일부 불량이 발생했지만, Zone B에서 품질이 회복되면서 배치 크기가 증가함.
- PDP 모델(d-f)은 고정된 배치 크기를 유지해야 하므로 품질이 좋아져도 배치 크기를 증가시키지 못함.
의미:
➡ HMM은 약간의 불량으로는 공정을 멈추지 않음, 불량이 나오더라도 공정 상태가 좋으면 계속 가동.
➡PDP는 불량이 발생한 후 대응, 사후 대응 -> 최적화에 한계가 있음.
최종 결론 – HMM 기반 배치 크기 조정 모델의 장점
1. 더 큰 배치 크기 유지 가능
- HMM 모델은 불량률을 낮추면서도 배치 크기를 최적화할 수 있음.생상성 향상!
2. 불량률을 사전 예측하여 빠르게 조정 가능 (Fast Stop)
- HMM 모델은 불량률이 증가할 것으로 예상되면 사전에 배치를 종료하여 품질을 유지함.
- 기존 PDP 모델은 기준 불량률을 초과한 후에야 조정이 가능하여 반응 속도가 늦음.
3. 공정 상태가 양호하면 배치 크기를 증가 가능 (Robustness)
- HMM 모델은 공정 품질이 양호한 경우 배치 크기를 증가시켜 생산 효율을 극대화할 수 있음.
- PDP 모델은 고정된 규칙에 의해 운영되므로 최적화할 수 없음.
4. 실시간 데이터 기반 최적화 가능
- HMM 모델은 실시간으로 공정 데이터를 분석하여 최적의 배치 크기를 조정할 수 있음.
- 기존 PDP 모델은 사전에 설정된 규칙만 따르므로 유연성이 떨어짐.
결론 – HMM 기반 배치 크기 조정 모델이 효과적인 이유
- 불량률을 낮추면서도 배치 크기를 최적화할 수 있음.
- "Fast Stop" 기능을 통해 사전 예측 및 배치 종료가 가능하여 불량을 최소화함.
- "Robustness" 기능을 통해 공정 품질이 양호할 때 배치 크기를 증가시켜 생산성을 극대화할 수 있음.
- 실시간 데이터를 기반으로 공정을 최적화할 수 있음.
➡ HMM 기반 모델이 기존 PDP 모델보다 더 효과적인 배치 크기 조정 방안을 제공함을 실험적으로 입증한다.